High Precision Injection Moulding: A Cornerstone of Modern Manufacturing
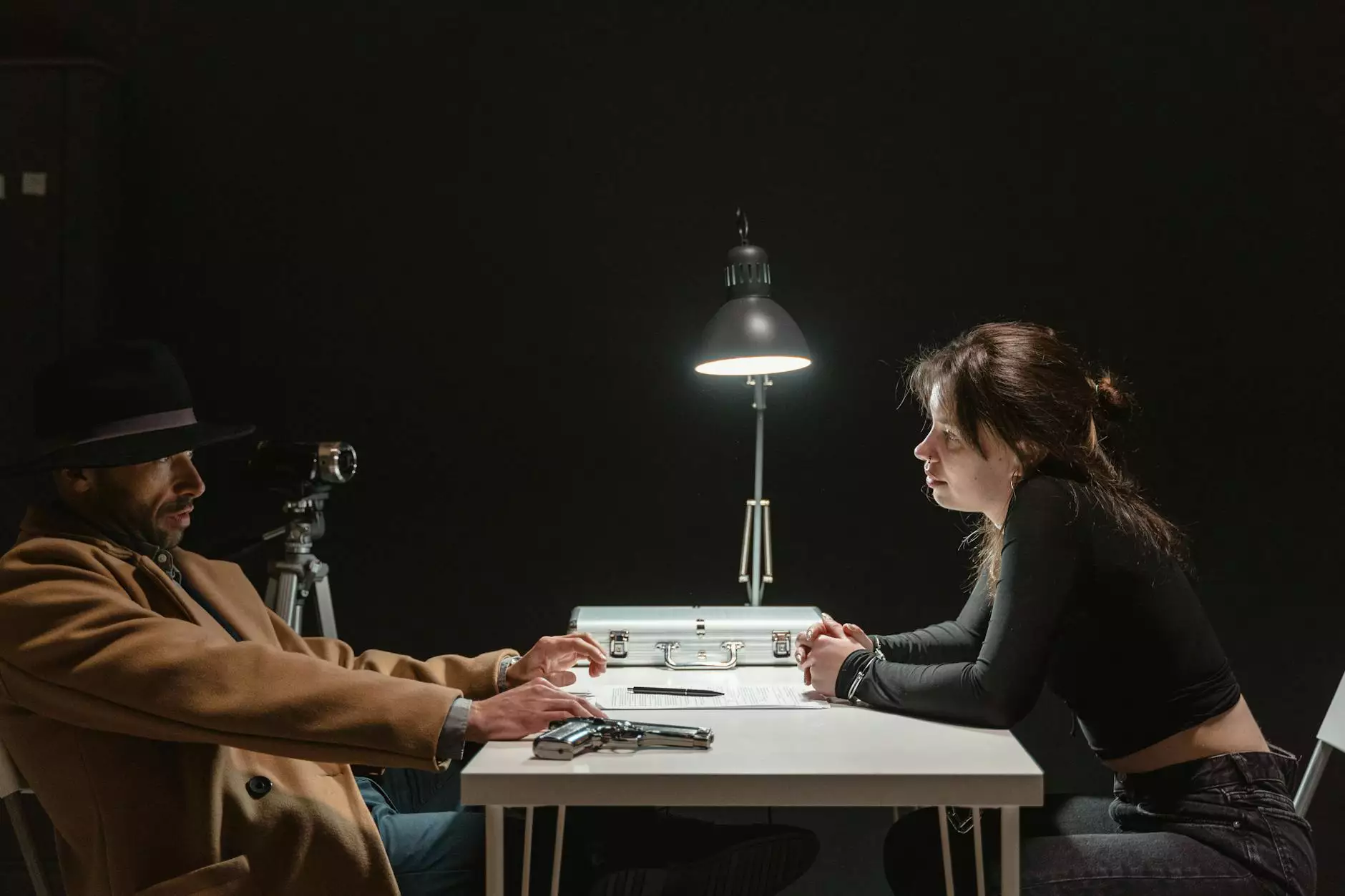
In today's fast-paced manufacturing environment, high precision injection moulding stands out as a transformative technology that elevates product quality and operational efficiency. This process enables manufacturers to replicate intricate designs with remarkable accuracy, making it an essential technique across various industries.
What is High Precision Injection Moulding?
High precision injection moulding is a manufacturing process where melted plastic material is injected into a mould cavity to create parts and products with tight tolerances and excellent repeatability. This technology is particularly revered for its ability to produce complex shapes with intricate details, all while maintaining strict adherence to dimensional specifications.
The Process of High Precision Injection Moulding
The injection moulding process involves several critical steps:
- Material Selection: Choosing the right type of plastic material based on the application's requirements, such as strength, flexibility, heat resistance, and appearance.
- Mould Design: Developing a mould that accommodates the intended part design while allowing for efficient material flow and easy release of the finished product.
- Melting the Material: The selected plastic is heated until it melts, allowing for smooth injection into the mould.
- Injection: The molten material is injected into the mould under high pressure to ensure that every contour of the design is filled.
- Cooling and Solidification: The injected material cools and solidifies inside the mould, forming the final product.
- Mould Release: Once the part has cooled and solidified, it is ejected from the mould with precision.
Benefits of High Precision Injection Moulding
The adoption of high precision injection moulding brings numerous advantages to businesses, including:
- Consistency: High precision ensures that every part produced is identical, eliminating variability.
- Efficiency: The ability to produce large quantities in a short time frame reduces labor costs and enhances throughput.
- Less Waste: Precise measurements reduce material waste, making the process more sustainable and cost-effective.
- Complex Geometries: Manufacturers can create highly complex parts that would be challenging or impossible to achieve with traditional manufacturing methods.
- Rapid Prototyping: High precision moulds can be quickly developed, allowing for faster iteration in design and testing phases.
Applications of High Precision Injection Moulding
The versatility of high precision injection moulding allows it to be utilized in a wide range of industries. Here are some notable applications:
- Automotive: Precision components such as dashboards, panels, and internal parts that require durability and exact fit.
- Electronics: Manufacturing casings and connectors that demand both aesthetic appeal and exact functionality.
- Medical Devices: Creating sterile and complex parts that meet rigorous health and safety standards.
- Consumer Goods: Producing everyday items that require high-quality finishes and appealing designs.
- Aerospace: Components that must withstand extreme conditions while adhering to strict regulatory standards.
Why Choose Deep Mould for High Precision Injection Moulding?
At Deep Mould, we specialize in providing high precision injection moulding services that help businesses streamline their production processes and enhance product quality. Our commitment to excellence is evident in every aspect of our operations:
- Expertise: Our team of experienced engineers and technicians possess deep knowledge of mould design and manufacturing processes.
- State-of-the-Art Technology: We utilize the latest machinery and software tools to ensure maximum accuracy in our moulding processes.
- Customization: We work closely with clients to tailor solutions that meet specific needs, from design to production.
- Quality Assurance: Every product undergoes rigorous testing to meet the highest standards of quality and performance.
- Competitive Pricing: We offer cost-effective solutions without compromising on quality, ensuring customers receive the best value.
Economic Impact of High Precision Injection Moulding
The economic implications of adopting high precision injection moulding are profound, affecting not just the individual business but also the wider industry landscape. Here are a few economic benefits:
- Cost Savings: The reduction in materials waste and labor expenses provides significant savings that can be reinvested in other areas of business.
- Job Creation: As manufacturing becomes more efficient, companies can scale operations, leading to job growth in the local economy.
- Innovation: Precision moulding allows for quicker development of new products, fostering a culture of innovation within industries.
- Global Competitiveness: Companies that leverage high precision moulding are often better positioned to compete on a global scale.
The Future of High Precision Injection Moulding
As we look to the future, the landscape for high precision injection moulding is set to evolve in ways that will further enhance manufacturing capabilities. Key trends to watch include:
- Advances in Materials Technology: New polymers and composites will enable even greater precision and performance for various applications.
- Increased Automation: Automated systems are expected to become more prevalent, reducing cycle times and improving precision.
- Integration with Industry 4.0: The incorporation of smart technologies, such as IoT and AI, will revolutionize the efficiency and effectiveness of moulding processes.
- Sustainability Practices: As environmental concerns deepen, sustainable materials and processes will become integral to injection moulding practices.
Conclusion: Embrace the Power of High Precision Injection Moulding with Deep Mould
In the competitive world of manufacturing, high precision injection moulding is more than just a production method—it's a strategic advantage. Companies that invest in this technology can achieve superior product quality, operational efficiency, and ultimately, a stronger position in the market.
Deep Mould is dedicated to helping your business thrive by providing top-notch moulding solutions tailored to your needs. Join us on this journey towards excellence in manufacturing. Contact us today to learn more about how we can support your business with our advanced high precision injection moulding services.