Understanding Lubrication Fittings: The Key to Efficient Machinery Maintenance
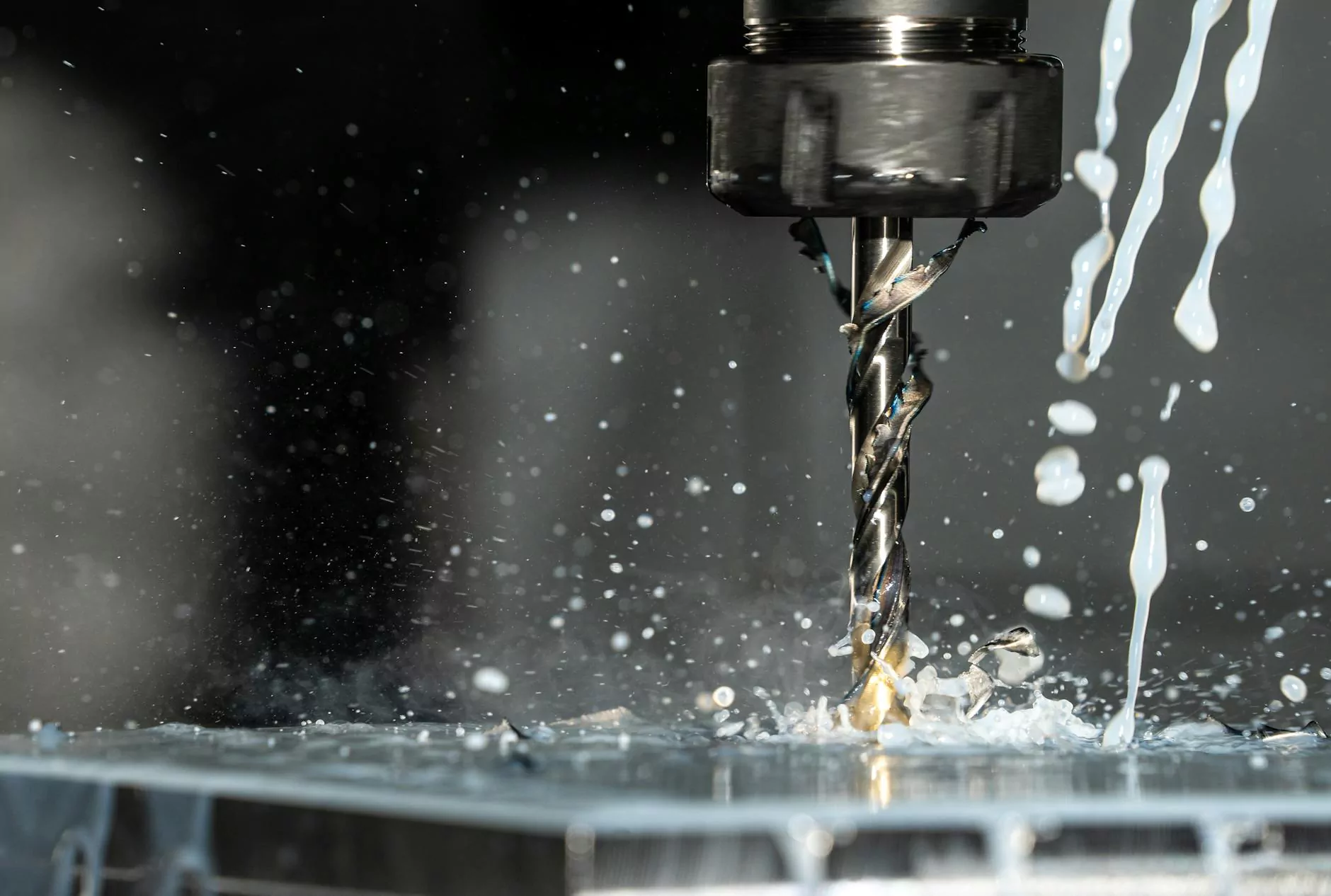
In the realm of machinery maintenance, one element stands out as critically important: lubrication fittings. These small yet essential components play a significant role in ensuring the longevity and efficiency of various mechanical systems. In this comprehensive article, we will delve deeply into what lubrication fittings are, their various types, and how to properly maintain them to ensure the optimal performance of your machinery.
What Are Lubrication Fittings?
Lubrication fittings, also known as grease fittings or zerk fittings, are connectors that allow the easy application of lubricant to machine components. These fittings enable the distribution of grease or oil to reduce friction and wear, ensuring that machinery operates smoothly and efficiently. Without proper lubrication, components would quickly wear down, leading to significant operational issues and costly repairs.
Types of Lubrication Fittings
Lubrication fittings come in various types, each designed for specific tasks and environments. Below are some of the most common types:
- Standard Zerk Fittings: The most common type, designed to accommodate a grease gun and allow for easy lubrication of moving parts.
- Button Head Fittings: Similar to standard zerks but with a more compact shape, ideal for installations where space is limited.
- Threaded Fittings: These fittings are typically used in applications where a secure connection is necessary to prevent leaks.
- Degreasing Fittings: Used for applications where quick disassembly is necessary, allowing for easy cleaning and maintenance.
- Blind Hole Fittings: Designed for use in places where access is not straightforward, providing a pathway for lubrication without requiring a direct line of sight.
The Importance of Proper Lubrication
Lubrication is a fundamental part of maintenance in almost every industry. Here are some critical reasons why proper lubrication is vital:
- Reduces Friction: By minimizing friction between moving parts, lubrication fittings help prolong the lifespan of machinery.
- Prevents Overheating: Lubricants dissipate heat generated by friction, preventing overheating that could result in mechanical failure.
- Minimizes Wear and Tear: Proper lubrication reduces wear on components, ensuring they function optimally for longer periods.
- Enhances Efficiency: Well-lubricated machinery operates more smoothly, increasing operational efficiency and saving energy.
- Reduces Noise: Adequate lubrication minimizes the noise levels produced by moving parts, enhancing workplace comfort.
How to Choose the Right Lubrication Fitting
Choosing the right lubrication fitting is critical to your machinery's maintenance and performance. Here are key considerations to keep in mind:
1. Determine the Lubrication Type
Understanding the type of lubricant you will be using, whether it’s grease or oil, is the first step. Some fittings are specifically designed for grease, while others may be suitable for oil or both.
2. Consider Operating Conditions
The environment where machinery operates plays a crucial role in determining the appropriate fitting. High dust levels, moisture, or extreme temperatures can affect the effectiveness of lubrication fittings.
3. Assess Accessibility
If a fitting is difficult to reach, it may be challenging to maintain proper lubrication. Ensure that the fittings you choose allow for easy access for grease guns or other tools.
Maintenance Tips for Lubrication Fittings
Regular maintenance of lubrication fittings is essential to ensure they function correctly. Here are some tips to keep in mind:
1. Regular Inspection
Schedule frequent inspections of your lubrication fittings to check for blockages, leaks, or any signs of wear. Early detection can prevent larger issues down the line.
2. Clean Fittings
Before applying new lubricant, clean the fittings with a cloth to remove any dirt or old grease that could interfere with the new lubricant's effectiveness.
3. Use the Correct Lubricant
Always use the lubricant recommended by the equipment manufacturer. Using the wrong type can lead to inadequate lubrication and potential machinery failure.
4. Monitor Lubrication Levels
It's essential to regularly monitor the lubricant levels in your machinery. Ensure that fittings are regularly filled to maintain optimal performance.
Where to Buy Quality Lubrication Fittings
When looking for high-quality lubrication fittings, sourcing them from reputable suppliers can make all the difference. FITSCH.CN offers a range of fittings that meet international standards, ensuring durability and reliability. Their extensive catalog allows you to find the right fittings for your specific machinery needs.
Conclusion
In conclusion, lubrication fittings are an often-overlooked yet crucial aspect of machinery maintenance. By understanding the types, selecting the appropriate fittings, and adhering to a stringent maintenance schedule, businesses can ensure their equipment performs efficiently, minimizing downtime and repair costs. Investing time and resources into this area will pay dividends in the longevity and functionality of your machinery. Explore the options available at FITSCH.CN and ensure that your machinery is properly maintained with the best lubrication fittings on the market.